PROFIMACH© HSVMC–III Series - New!!
High speed bridge type vertical machining centers
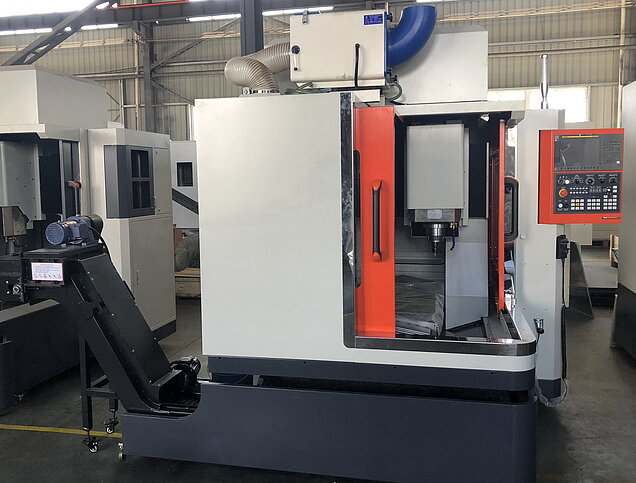
PROFIMACH© HSVMC–III Series vertical machining center
High precision and flexibility for Electrode, Mold & Die machining
The use of high speed milling in moldmaking shops is no longer viewed as merely providing a firm with a competitive advantage. It is a disruptive technology that is becoming a competitive necessity. It is now being employed extensively, and those mold shops not effectively implementing this technology could fall by the wayside in the highly competitive worldwide marketplace.
Walk into any die/mold shop and you’ll find dedicated machines for wet and dry hard milling and graphite milling, three common operations. Die/mold shops often run dedicated hard milling and EDM machines for these operations because each has special requirements.
Mounting the pressure to minimize costs, while improving machine and spindle utilization will force many machine shops to consider investing in machines with multi-purpose use or so-called all-in-one machines like our HS-VMC Series. The PROFIMACH© HSVMC–III Series (High Speed Vertical Machining Centers) are designed with a thermal- symmetric bridge type structure to optimize precision and workpiece quality. High accuracy is also enhanced by the constant pre-load high speed spindle.
All-in-one vertical machining centers such as our Profimach HS-VMC Series, with graphite, copper and steel milling capability, have wet and dry hard milling capabilities but can also be configured for milling graphite. Using these machines, die/mold shops can lower their costs by reducing downtime, training and maintenance spend. In addition, shops can decrease lead-times and improve machine and spindle usage.
Profimach HSVMC-III Series
Premium Line Third Generation High Speed Vertical machining Centers
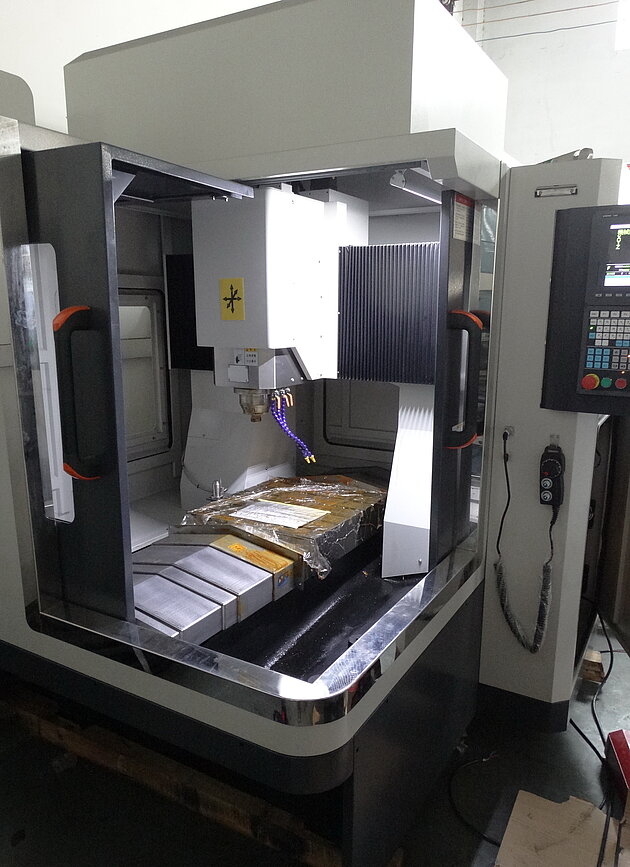
Profimach HSVMC-6050-III
Premium Line High Speed Milling center
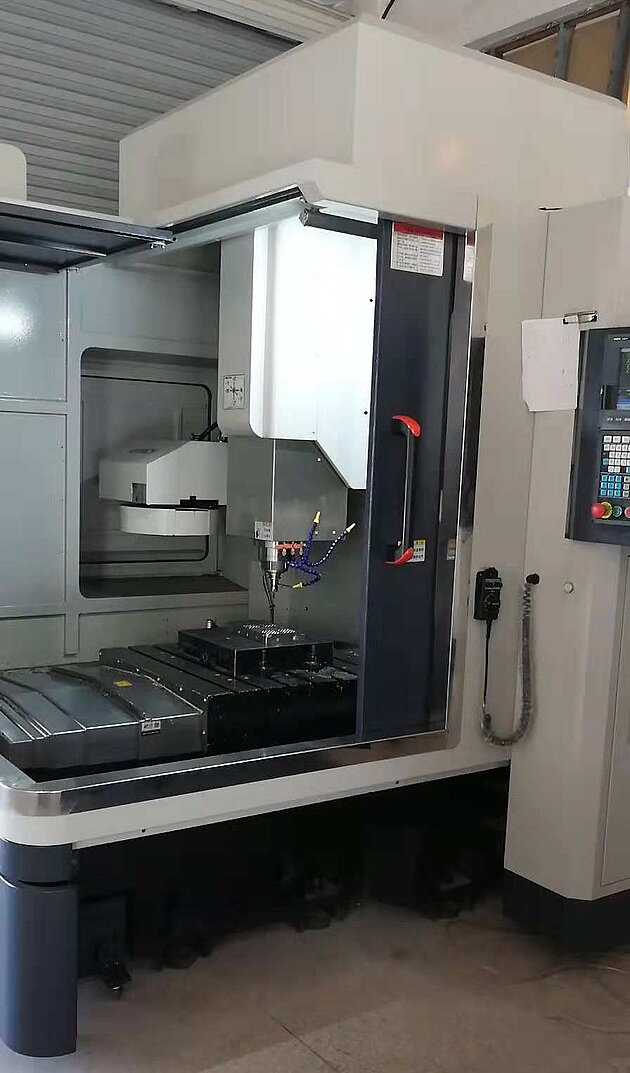
Profimach HSVMC-8080-HD -III
Heavy Duty Premium Line high speed Vertical machining center
High Speed vertical machining center : HSVMC
Special Mold and dies
Profimach's high speed milling CNC equipment will give you capabilities that you never dreamed of. Whether you’re making molds to produce components for aerospace, electronics, medical automotive or telecommunications, you need to use small tools and a means of running them with efficiency.
Frequently, making these molds requires EDM electrodes that present challenges to the process of micro milling. Not the least of which is the fact that polishing and handwork is not practical where these intricate parts are concerned – so a quality surface finish must come from the machining process itself.
SPECIFICATIONS:
MACHINE | UNIT | HSVMC-5060-III | HSVMC-6070-III | HSVMC-8080-III | HSVMC-80100-III |
---|---|---|---|---|---|
Worktable size | mm | 500*600 | 700*600 | 800*800 | 800*1000 |
Max. X × y × z travels | mm | 500*600*260 | 700*600*260 | 800*800*400 | 800*1000*400 |
Spindle nose to worktable distance | mm | 50-310 | 30-290 | 70-470 | 70-470 |
Distance between columns | mm | 650 | 650 | 880 | 880 |
Max. Workpiece load | kg | 300 | 300 | 400 | 400 |
Max. Moving speed | m/min | 32/32/32 | 32/32/32 | 32/32/32 | 32/32/32 |
Max processing speed | m/min | 12 | 12 | 12 | 12 |
Positioning accuracy | mm | ±0.005/300 | ±0.005/300 | ±0.005/300 | ±0.005/300 |
Repeatability | mm | ±0.003 | ±0.003 | ±0.003 | ±0.003 |
Spindle motor power | kW | 5,5 | 5.5 | 5,5 | 5.5 |
Max. Speed of spindle | rpm | 3000-24000 | 3000-24000 | 3000-24000 | 3000-24000 |
Spindle taper | code | BT 30 (opt ER32) | BT 30 (opt ER32) | BT 30(opt ER32) | BT 30(opt ER32) |
ATC tool capacity | pcs | 12 (rotary type) | 12 (rotary type) | 12 (rotary type) | 12 (rotary type) |
Overall size | mm | 1950*1895*2355 | 1950*1895*2355 | 2450*2150*2675 | 2750*2150*2675 |
Weight | kg | 3480 | 3840 | 5120 | 5450 |
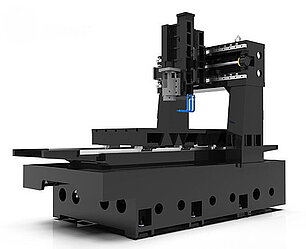
Optimal structural design
Bridge-Style High Speed Vertical Machining Centers
- Main mechanical structures, such as: base, column, saddle, etc., are made of Meehanite casting iron with the process of heat treatment to release the residual stress to ensure every actual miniature movement and to maintain a long-lasting accuracy.
- Box-shaped structural design on beam, together with ladder-like layout of linear guideway makes the combining span of saddle wider and assures a powerful and stable machining capability on the spindle.
- The no-counterweight structural design on headstock is without stagnant phenomenon caused by inertia and no vibration resulted from the counterweight, but with the agile, quick and stable response in feed.
- 3-axis ballscrews, being pre-stretched, can effectively refrain from the thermal deformation and surely guarantee the precise positioning accuracy and repeatability accuracy.
- All components made by casting iron are through special treatment to release internal stress so as to assure good accuracy in long-term operation and long service hours.
HSVMC Bridge type vertical milling machines
By using a bridge construction, this vertical milling machine becomes five times more rigid than a traditional "C-Frame" style VMC

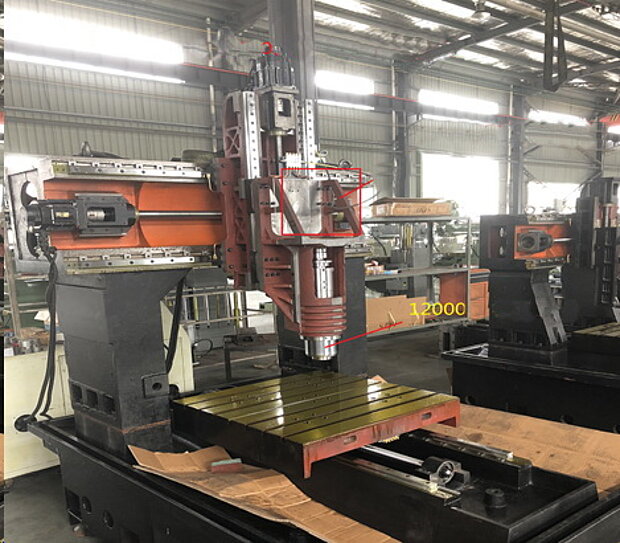
Rigid Bridge Column Type Construction
The characteristic twin bridge & column of our HSVMC has been FEM calculated and it’s made of one-piece Meehanite, high quality casting. This design insures maximum rigidity and performance in High Speed milling and reduces vibrations during heavy cutting operations. Thermal influences are minimized, due to the short distance between spindle axis and the portal structure.
Thermal analysis of the symmetrical structure proves that this is the optimal solution for high precision machining of mild products. Full cast iron structure has been stress-relieved giving the machine maximum stability, accuracy and repeatability.
No-counterbalance design on headstock
- The no-counterweight structural design on headstock is without stagnant phenomenon caused by inertia and no vibration resulted from the counterweight, but with the agile, quick and stable response in feed.
- Z-axis linear guideway with rigid precisie guiding blocks ensures good accuracy in long-term operation and long service hours.
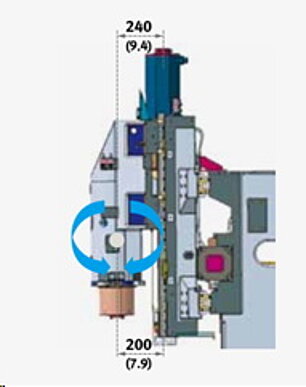
Gravity Center Drive Structure
By minimizing the distance between gravity center and the feed drive center, the inertia movement is reduced allowing for faster feed rates and a more precise part.
High quality special casting FCD45 is used on saddle and ram, to get the fastest and most precise feed response on Z axis movements.
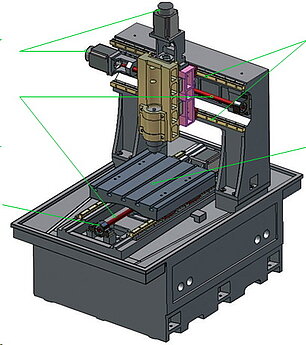
Only the highest quality components
Roller type Guideways
Japan/Taiwan high rigidity and heavy-duty roller type linear motion guideways on 3 axis, provide low starting inertia, low friction and high acceleration rates. Servo motors and drives are optimized to ensure immediate &precise machine response necessary in high speed cutting, positioning and contouring.
User-Friendly & Ergonomic guarding design
The design of the guards allows for optimum viewing of the part being machined. Totally enclosed guarding includes roof top/side to keep all the chips, water and noise inside the machine and to have clean, quiet and comfortable environment also around the machine. The machine has been carefully designed to provide a reduction of overall floor space dimensions.
Automatic Tool Changer
Disk Type 12 station automatic tool changer installed as standard.
Hand scraping Precision
Only the best craftsman can guarantee you this perfect allignement
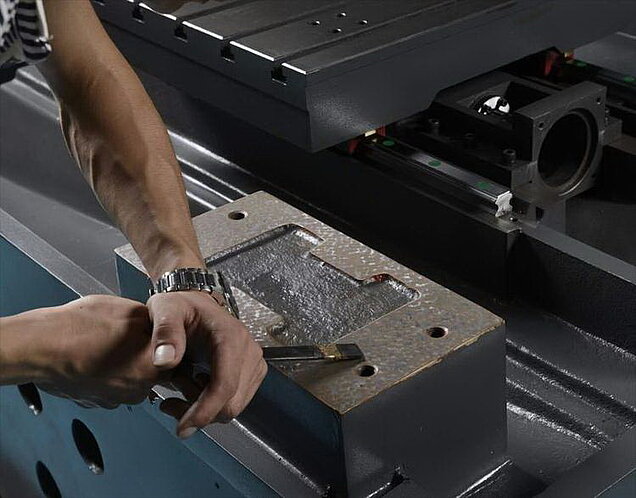
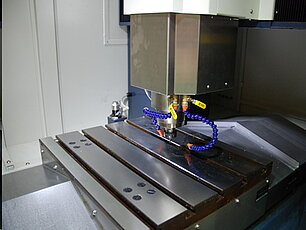
Table – Wide cutting Area
The size and load capacity of the table allow the setting up and cutting of larger workpieces of various shapes. Table is 100% fully supported during full stroke of the Y-axis. X-axis is on the bridge.
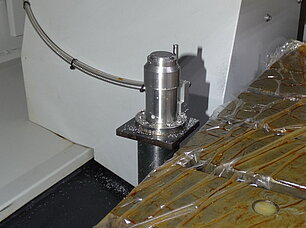
Automatic tool length measurement standard
Saves precious time and improves your quality
Tool steel is not the easiest material to cut. One of the greatest difficulties encountered when machining hardened tool steels is that cutter wear can reach unacceptable levels within the time required to machine a single, multi-featured electrode. As such, to help mitigate the effects of cutter wear, the use of tool measurement probes on the machine tool is highly recommended. Tool length measurement probes, are particularly helpful when it comes to validating the length of cutting tools and tracking their wear state.
We have each machine standard equipped with an automatic tool length measuring device.
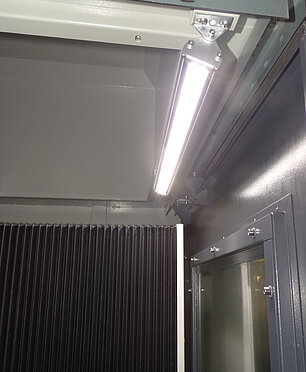
Interior high efficient and economic LED lighting
Saves energy and gives bright and clear interiors
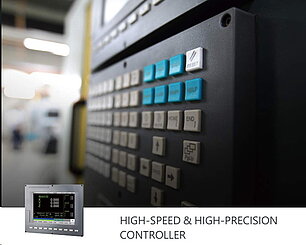
SUPER HIGH SPEED CNC controller
0,4 µsec block processing time - 2500 blocks/second processing speed - 2000 Blocks look ahead
Powerful Controller with Mechatrolink M3 Bus Protocol
SYNTEC/Mitsubishi 21/22MA controller comes with serial bus Mechatrolink-III connection motion control, improves machining performance by decreasing interpolation time and increasing surface’s smoothness. Serial bus communication control also improves traditional pulse delay of differentiate transfer time between axis, provides a simpler system and easier to install and setup.
High Speed, High Precision, High Quality
SYNTEC 21/22MA controller is equipped with 2500blocks/sec. computational ability, 2000 block look ahead function and High Speed - High precision feature, such as SPA, HPCC, surface smoother, quick parameter setup, high speed tapping, multiple spindles synchronize motion tapping etc.
SYNTEC 21/22MA is definitively the best solution for high efficiency and high precision mold machining. For 5 axis the Block processing time becomes 4000 blocks per second = 0,00025 sec/block reading time (0,25µsec)
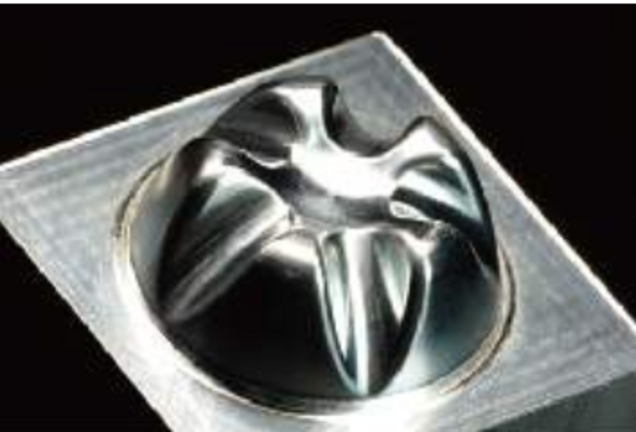
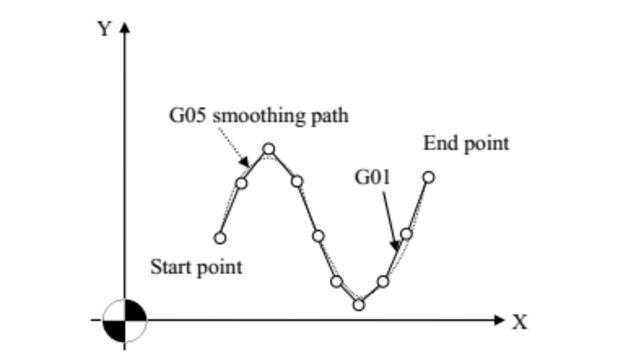
High-Speed, High-Precision Machining (HSHP) function
High-Speed, High-Precision Machining (HSHP) function included
The HSHP function (Mode I and mode II) in the dedicated mold making controller can process 2500 blocks/sec (program lines) and look-ahead 2000 blocks each second. These enable smooth motion and enhance surface quality. To advance the precision, the included HSHP function also controls the corner and arc feed-rate efficiently.
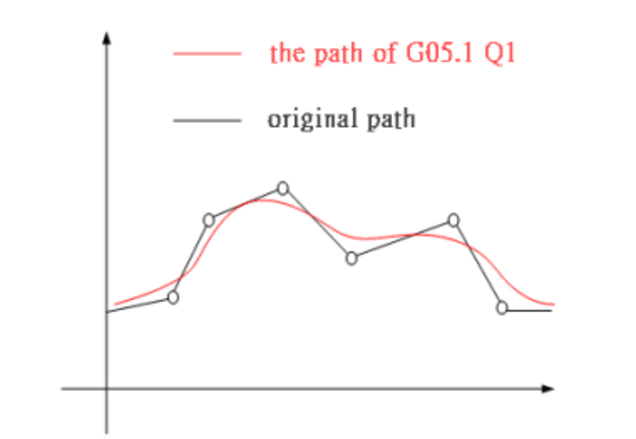
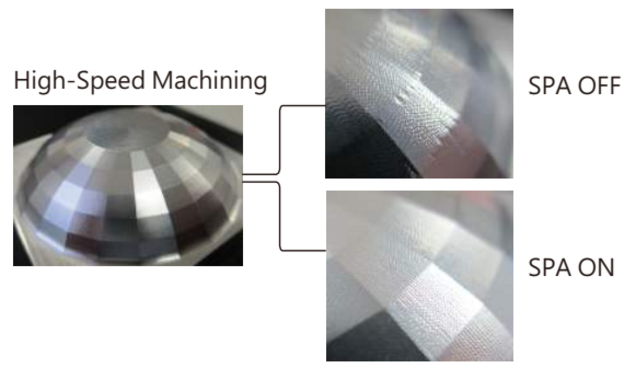
Smooth Precision Advanced (SPA) Function
Smooth Precision Advanced (SPA) Function included
Due to limitation of machine condition, servo mismatch can be found even the servo loop gain has been optimized. This error causes dimensional shrinkage especially in high-speed machining. SPA feature is designed to overcome this issue.
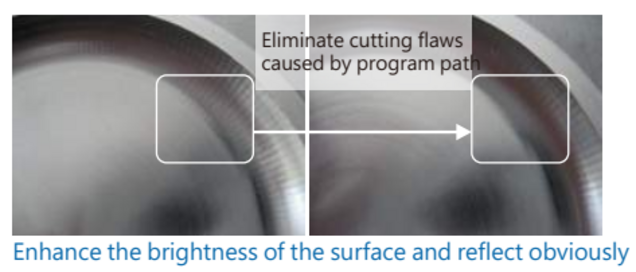
Path Smoothing Feature
Path Smoothing Feature included
By trimming the rough program path generated by CAD/CAM software with a tolerance, the desired smooth and fine path is estimated by Path Smoothing function. This improves the surface finish, machining efficiency and stability of machine tool.

High Precision Contour Control (HPCC) function
High Precision Contour Control (HPCC) function included
The tool path generated by CAD/CAM software is generally discontinuous, and it causes negative effects on machining operations. The problems will be more serious because of larger CAD/CAM tolerance. HPCC function fits the discontinuous blocks into a smooth-curve path, and this will enhance the machining precision and reduce the mechanical shock.
Optional high speed 4 and 5 axis milling
With Direct Drive Rotary tables
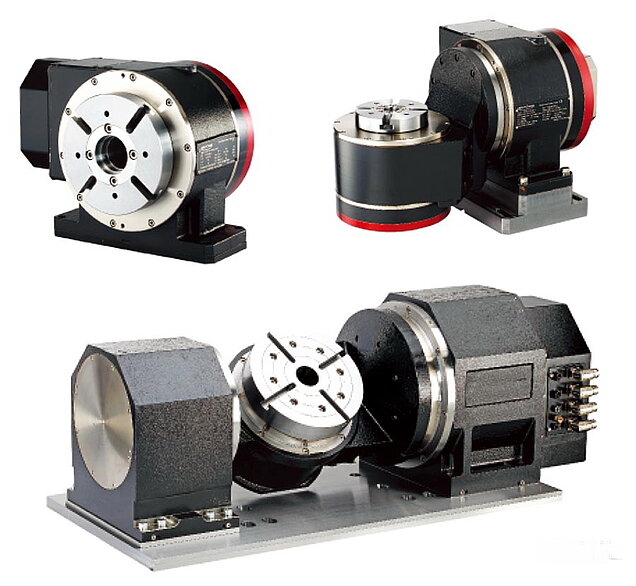